Image Credit: 2024 Gianpaolo Palma, Narges Pourjafarian, Jürgen Steimle, Paolo Cignoni
Unveiling a groundbreaking leap in 3D touch technology, the SIGGRAPH 2024 Technical Paper “Capacitive Touch Sensing on General 3D Surfaces” marks a significant breakthrough in 3D touch technology, redefining mutual-capacitive sensing to deliver high-resolution, robust, multi-touch capabilities on complex surfaces. Contributor Gianpaolo Palma shares insights into this transformative approach. Explore how these innovations streamline sensor layouts and enhance touch sensitivity, poised to revolutionize touch-sensitive devices.
SIGGRAPH: Share some background about “Capacitive Touch Sensing on General 3D Surfaces.” What inspired this research?
Gianpaolo Palma (GP): The research was inspired by my previous work on using 3D-printed tangible user interfaces in virtual reality (VR) applications. The primary goal of that previous project was to provide users with tactile feedback from a 3D-printed object while they manipulated its virtual counterpart in the VR environment; this could be, for example, enabling the virtual painting of an object with engaging tactile feedback. Therefore, we were required to accurately detect touch positions on the object, and we implemented it by integrating two distinct technologies: active hand tracking with ray casting to determine where the user touched the surface and self-capacitance sensing to detect when the touch occurred. While the final application was impressive, the integration and calibration of these technologies resulted in an average spatial touch accuracy of approximately 1 cm. In certain situations, accuracy deteriorated even further. This led to a natural question: Is there a more precise and accurate solution for determining touch positions on complex 3D surfaces? After reviewing the current state of the art, I observed that while some solutions have been proposed for making 3D surfaces interactive, achieving high-touch accuracy on large, highly irregular surfaces was still an open problem.
SIGGRAPH: What inspired you to explore the extension of mutual-capacitive sensing technology to complex 3D surfaces, and what were the main challenges you anticipated at the outset of this research? How did you overcome them?
GP: Mutual capacitive sensing is one of the most robust technologies for detecting touch in everyday interactive devices such as smartphones, tablets, and smart appliances. Extending this technology to complex 3D surfaces appears as a natural evolution, but actually implementing high-resolution, multi-touch sensing to general 3D shapes presents three key challenges. The first challenge is distributing the sensor grid as uniformly as possible across the 3D surface. The paper proposes a method based on a quad mesh approximation of the surface, followed by a quad patch layout simplification and clustering. This approach minimizes the number of exit electrodes from the object and reduces the required touch controllers. The second challenge is routing the electrodes through the internal volume of the object to connect the surface sensors to external touch controllers. We propose an optimized routing algorithm that accounts for the object’s volumetric constraints and minimizes electromagnetic interference between the electrodes. The final challenge is the physical fabrication of the prototypes. We overcame this through a semi-automated process, though there are opportunities for future improvements. This opens new research avenues for advancing fabrication techniques. However, the success of this work was made possible by integrating complementary expertise, particularly in geometry processing and human-computer interaction, from the Visual Computing Lab at ISTI-CNR and the Human-Computer Interaction Lab at Saarland University.
SIGGRAPH: Your research mentions a new simplification and clustering algorithm for electrode quad layout. Could you explain how this algorithm works and its significance in the overall process?
GP: The first challenge in our project is to distribute the electrodes for capacitive touch sensing across a general 3D surface as uniformly as possible. This aims to minimize both the number of touch controllers required to sensorize the surface and the number of conductors needed to connect the electrodes on the surface to the controllers. The primary objective of our simplification and clustering algorithm for quad patch layout is to reduce the number of conductors and controllers, making the physical fabrication of the touch-sensitive object feasible. The simplification algorithm focuses on subdividing the quad mesh approximation of the surface into the fewest number of large quad patches that can be easily mapped to the rectangular sensing regions of each controller. This algorithm is based on simple observations about the quad patch layout construction for 3D surfaces and employs specific rules to eliminate very small patches, all encoded in a novel integer linear programming formulation. The clustering algorithm aims to compact the quad patches while preserving their proximity to minimize the number of touch controllers and conductors. Although our proposed solutions may, in some cases, require slightly more controllers than the trivial solution derived from a 2D bin packing algorithm, they significantly reduce the number of conductors within the object’s volume. This ensures a feasible and practical fabrication process while effectively connecting the surface sensors to the controllers.
SIGGRAPH: What were some of the most exciting or unexpected findings you discovered while characterizing the signal quality and spatial accuracy of the capacitive touch sensors?
GP: The most exciting result was the high signal-to-noise ratio (SNR) values and the exceptional spatial accuracy achieved by the prototypes that we built using just off-the-shelf technologies and components. In particular, the spatial accuracy of approximately 1 mm was completely unexpected and remained consistent across all tested prototypes and geometric configurations. In only a few instances, such as on very sharp edges and corners, the spatial accuracy decreased due to sub-optimal sensor placement, an issue that can be addressed with a more straightforward and practical approach. These impressive results were achieved despite the semi-automated fabrication process, which can introduce additional uncertainties. This gives us hope that we could further improve these results with a fully automated and more controllable fabrication process.
SIGGRAPH: How do you envision this research being used in the future?
GP: Our research can benefit any application where transforming everyday surfaces into interactive devices with highly accurate touch detection provides an advantage. One example is the entertainment industry, where it could enable the development of more interactive gaming devices and controllers that offer precise and localized feedback, or new tangible interfaces for virtual object painting. Another promising field is the automotive industry, where creating more engaging, interactive surfaces opens up new design possibilities. In general, the ability to sensorize any 3D surface allows for more innovative design solutions, breaking free from the current limitations of flat or single-curvature surfaces.
SIGGRAPH: What advice do you have for those submitting to SIGGRAPH Technical Papers in the future?
GP: Don’t be afraid to push your most creative and groundbreaking ideas. Focus on clear writing, engaging figures and diagrams, and a compelling demo that showcases how your concept goes beyond the boundaries of what’s possible. Let your innovation shine with confidence.
Can’t get enough of the Technical Papers presented at SIGGRAPH 2024? Check out the SIGGRAPH 2024 Technical Papers Awards blog to see the groundbreaking research shaping the future of computer graphics and interactive techniques.
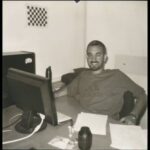
Gianpaolo Palma is a researcher at the Visual Computing Lab at ISTI-CNR in Pisa, Italy. He graduated in 2008 and received a Ph.D. in Computer Science at the University of Pisa in 2013, working on acquiring and rendering the surface appearance. His research interests focus on computer graphics, with a particular emphasis on point cloud rendering and analysis, geometry processing, and 3D printing.